It is not easy to briefly explain the most common engraving techniques used throughout the ages (from the XV century up to the present days). We will nonetheless try to give the major outlines of the procedures adopted by the great masters.
Printmaking techniques can be divided in the following three groups:
RELIEF PRINTING – INTAGLIO PRINTING – PLANOGRAPHIC PRINTING
Relief printing
It owes its name to the fact that prints are obtained using metal or wooden plates engraved in relief. The printing-ink is applied only on the parts that must be impressed on paper. Pressure is exerted vertically downwards by means of a press or manually using a roller or a brayer. The most famous technique of relief printing is the “xylography”, made on wood. Using a sharpened tool those areas of wood that will be “white” on paper are removed, while the parts standing in relief are inked. In ancient times resistant wood like apple, pear or cherry wood was used for this kind of printing so that the plates would not cleave easily.
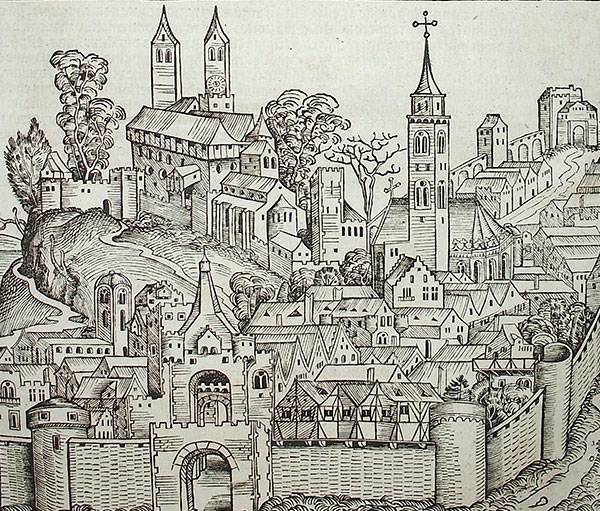
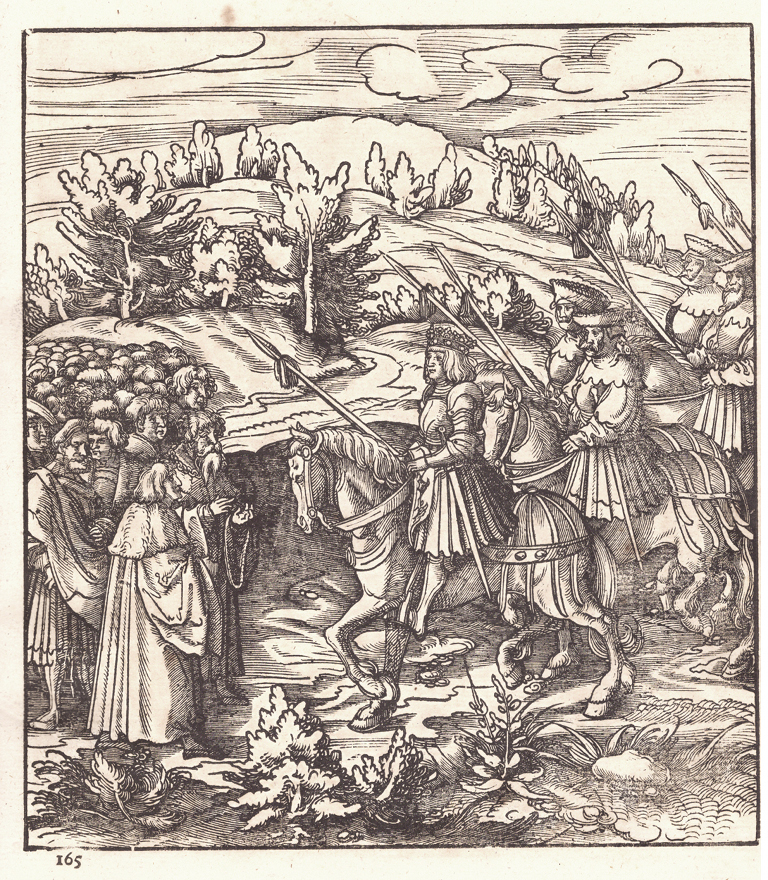
Intaglio printing
Intaglio prints are obtained by engraving with a burin or etching a metal plate. The drawing to be reproduced is carved in metal. Printing-ink is applied in the grooves while the parts that must result white are carefully cleaned.
Burin engraving (direct process)
The burin is a thin quadrangular steel bar ending with a sharp point cut crosswise. It is used to engrave directly on copper. During engraving, the burin raises a thin metal foil, called “burr”, before and along the groove. The burr is then removed with a scraper to obtain clear lines which are typical of this kind of printing.
Drypoint
This technique is usually combined with etching. The engraver sketches the drawing with a stylus used like a pencil. Burrs remain only along the furrow and will not be removed with a scraper as in the burin engraving.
Etching (indirect process)
It is called “indirect process” because the line is not incised by the hand of the artist, but etched in acid. The copper is covered with a thin layer of varnish. The plate is then blackened with lampblack to make the drawing more visible. The engraver uses a steel stylus to carve the design, exposing the copper to be printed. The plate is afterwards immersed in some diluted acid which corrodes the metal where the varnish has been removed. Lines can be more or less deep depending on the length of the bath. This procedure can be repeated for several times, and while the completed parts are protected with another coat of varnish, those needing changes can be engraved again.
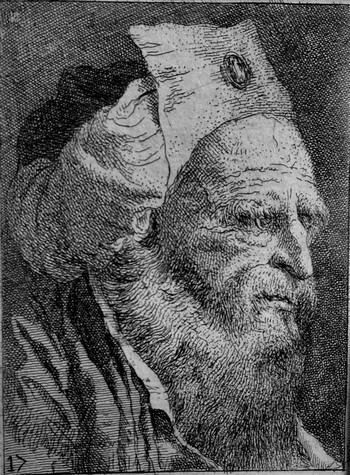
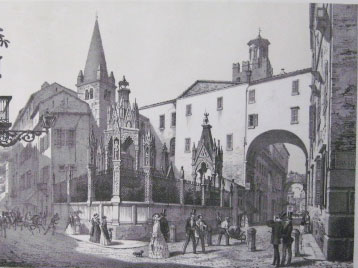
Planographic printing
The secret of this technique lays in the incompatibility between grease and water and in the capacity of limestone to absorb both grease and water. The artist draws the design with a special greasy crayon on a polished piece of limestone. The stone is then bitten by acid to fix the crayon lines. Later the plate is flooded with water and rolled with printing-ink. Ink is repelled from the watersoaked areas and absorbed only by the drawn design.